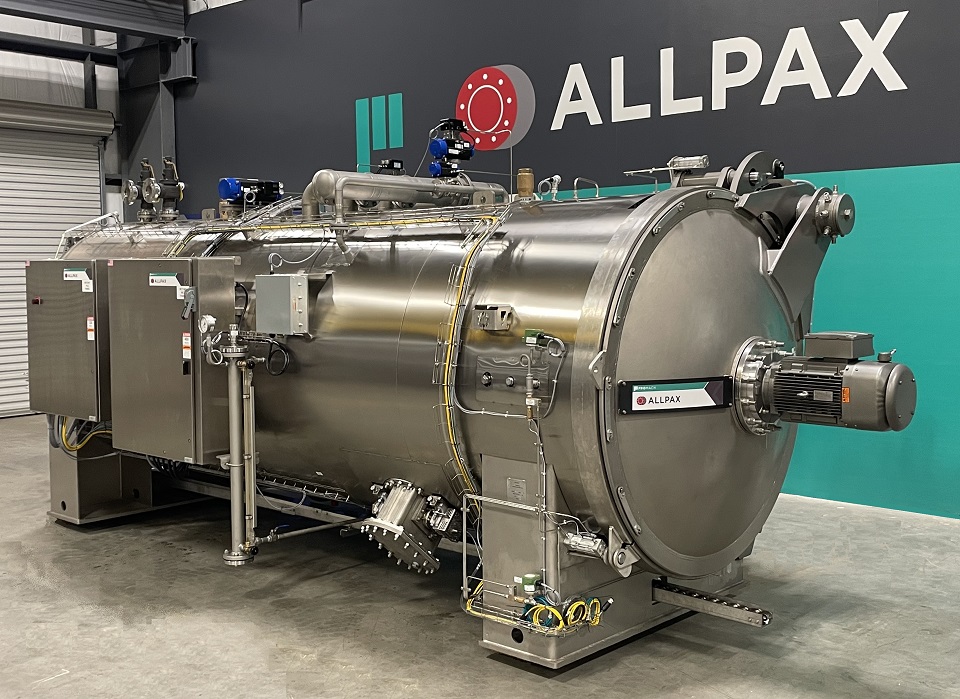
The Steam-Air process is an overpressure process, like water immersion, and water-spray, except that the product is exposed to the influence of the overpressure air. Because overpressure air enters the retort with steam, and steam is the only heating medium, a large fan is used as a driving force to mix the steam with the air, to prevent cold spots in the machine. The fan is used in conjunction with a baffling arrangement inside of the retort to channel the heated steam-air mix to the center of the retort load.
Note on Terminology
In the Allpax retort control system there is terminology for an Uncleared Deviation or a (Cleared) Deviation condition that may exist. These terms are referred to in this paper. The definitions of these terms are as follows:
- CLEARED DEVIATION – When a deviation occurs, it may be possible to correct the process by adding time and/or temperature in order to compensate for the deviation. If this correction can take place in the retort, then the batch is declared to have a Cleared Deviation status. The Cleared Deviation status notifies the retort operator that a deviation was detected, but that corrective action was taken to compensate for the deviation (see Scheduled Process / Alternate Process definition). As in all cases, release of the product is subject to final review by the plant’s Quality Manager or Process Authority.
- UNCLEARED DEVIATION – When a deviation occurs in which an unsafe product condition exists and cannot be corrected for, then the batch is declared to have an Uncleared Deviation status. The Uncleared Deviation status notifies the retort operator that a deviation was detected and continues to exist in the batch.
Process Steps
Batch retorts execute a series of programmed process steps (also known as segments). These steps must be properly executed to achieve a sterilization process that meets the regulatory requirements imposed for food safety.
In a Steam-Air process these steps are:
- Come Up Vent Open (A Sterilization Step)
- Come Up Vent Closed (A Sterilization Step)
- Cook (A Sterilization Step)
- Pressure Cool Fill – [Optional – see notes]
- Pressure Cool
- Atmospheric Cool
- Drain
Click the above image to see an animation of the Rotary Steam/Air process
The following is a detailed description of each step:
VESSEL PURGE – STEAM-AIR
This is an optional step in a steam-air process, and may be eliminated in some retort processes. The purpose of this step is to introduce steam into the vessel and to minimize the air that is in the retort. This step is accomplished by opening the vent valve and opening the steam control valve (and, if configured, opening the steam bypass valve). An established vent time and temperature has been determined for the retort and product that is being processed. Since venting is both retort and product-specific, each product may have its own vent schedule, which will be incorporated into the product recipe. This information has been filed with the appropriate regulatory agency (FDA or USDA).
In order to successfully complete this phase, both time and temperature conditions, established in the recipe must be met simultaneously. At the end of the scheduled vent time, the retort must be at, or above, vent temperature. If these conditions are not met, the vent time may be extended so that the vent temperature can be reached, without creating a deviation. Should the actual process be advanced to the next process step without satisfying both conditions simultaneously, then an Uncleared Deviation condition is created.
It is also imperative that the vent valve be open for the entire vent step. An open switch on the vent valve is provided for this positive indicator, as well as a vent closed switch. Should the vent open switch be seen as “not made,” or the “vent closed” switch be seen as “made,” or if both switches are seen as both “made,” at any time during the Vent Step, an Uncleared Deviation condition is created.
If water in the retort is detected at a level that is high enough to reach the bottom of the retort basket, an Uncleared Deviation condition is created.
COME UP VENT CLOSED – STEAM-AIR
During this step, the vent valve is closed and the temperature is controlled and ramped to Cook Temperature (unless multiple Come Up Vent Closed steps are utilized.) The Fan continues to be controlled to its setpoint. In order to successfully complete this phase, both time and temperature conditions, established in the recipe must be met simultaneously. At the end of the scheduled come-up time, the retort must be at, or above, scheduled cook temperature. If it does not meet these conditions, the step time may be extended so that the recipe temperature can be reached, without creating a deviation. Should the actual process be advanced to the next phase without satisfying both conditions simultaneously, then an Uncleared Deviation condition is created.
If water in the retort is detected at a level that is high enough to reach the bottom of the retort basket, an Uncleared Deviation condition is created.
COOK / HOLD / STERILIZATION – STEAM-AIR
The purpose of the Cook Step is to maintain the recipe temperature for the time required by the recipe. In order to successfully complete this step, the temperature condition established in the recipe (the filed process) must be met for the length of time defined for the step. The fan remains on. Should a temperature drop occur at any time during the step, then a temperature deviation condition is created. Should an alternate process be available when a temperature deviation occurs, then the batch is labeled as a Cleared Deviation. Should the alternate process(es) not be successfully administered, then the Uncleared Deviation condition for the batch is created.
During this step, the operator is required to make operator entries: at least one check and entry of the MIG reading entry, one for the Chart reading, and one for the Bleeder Valve check. All operator entries must be made for the step to be completed.
During the Cook Step of a steam-air process, the batch may be declared a Temperature Deviation or an Uncleared Deviation after the MIG / RTD comparison check is made.
During the Cook Step of a steam – air process, the batch would be declared an Uncleared Deviation if water is detected at a height sufficient to reach the bottom of the basket.
PRESSURE COOL / ATMOSPHERIC COOL – STEAM-AIR
The fan is turned off and is not used for the remainder of the process.
Note: The Steam-Air retort may use a flooded cooling step or a spray cooling step. If flooded cooling is used, see the documentation in this book for Pressure Cool Fill – Saturated Steam through to Atmospheric Cool – Saturated Steam. If spray cooling is used, see the documentation in this book for Pressure Cool – Water Spray through to Atmospheric Cool – Water Spray.
DRAIN – STEAM-AIR
This step drains the water from the retort. The drain is opened the water gravity-drains from the retort. When the level condition is met, the step ends. Note: To accelerate the drain step, limited overriding air pressure (2-5psi) may be used during the step.
A complete line of retort room equipment, including water immersion (rotary) retorts. See Allpax Steam-Air Retorts.