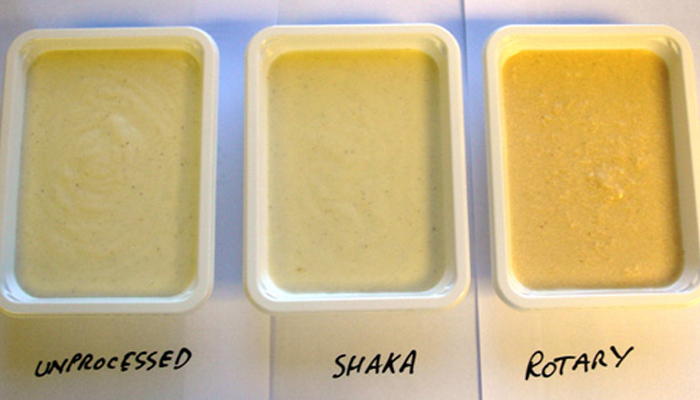
In the standard model of low-acid shelf-stable food processing, Ultra High Temperature (UHT)/aseptic packaging and retort sterilization are clearly differentiated in terms of the types of food processed, packaging used, and business models for which each is best suited. Now the Shaka® retort process blurs the lines between UHT/aseptic packaging and retort sterilization, making it possible for a processor to produce UHT quality food through a batch retort process that has a significantly lower capital and labor cost; faster time to market, including validation; and greater flexibility than UHT processing.
The Shaka® process
The Shaka® retort agitates packaging using a six-inch double-stroke reciprocating movement at speeds greater than 100 double strokes per minute. The intense horizontal back and forth movement is equivalent to as high as 2-3 gs of force, which creates a uniform internal heat map within the package. In the Shaka® basket, packaging is oriented horizontally with cans, pouches, and trays parallel to the direction of movement. The rapid agitation in effect eliminates the traditional cold spots. The size of the package does not affect heat transfer: thermal distribution is equal top to bottom and front to back. Air bubbles disrupt surface oxidation/burning and, as this video shows, actually dig into the product, facilitating thermal distribution (See short video).
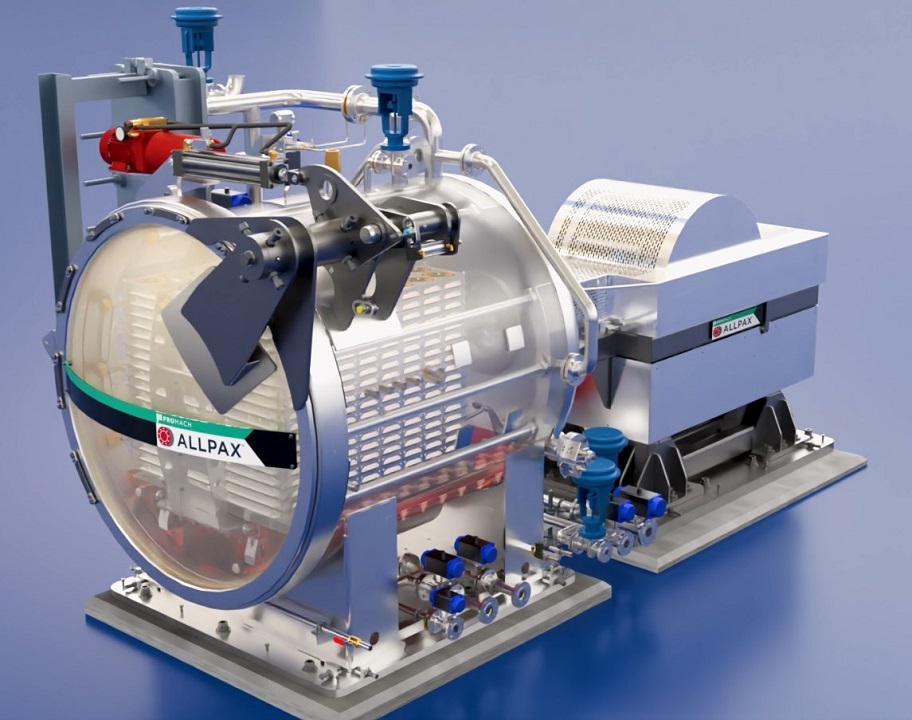
Click the above image to view an animation of the SHAKA® retort Process
Testing has shown that the sweet spot for Shaka®-style agitation – lowest sterilization time – is between 100 to 180 six-inch double-reciprocating strokes per minute. For example, 400 gm cans of vegetable soup heated to 250˚ F in a static retort require about 50 minutes of sterilization time. At a Shaka® agitation of 180 reciprocating double strokes per minute, process time reduces by 90 percent to 5 minutes. The significant drop in heating and cooling time leads to a higher quality product in terms of taste, appearance, and texture.
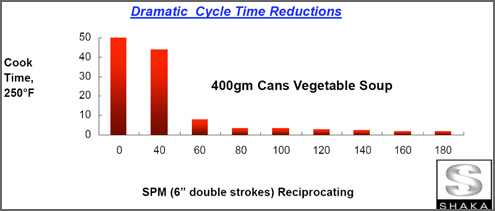
Although the Shaka® process patent was developed by British firm Zinetec Ltd. a number of years ago and licensed to Allpax, it required five years of research and development to bring a production model to market. The production unit, as shown in this Shaka retort production video is a single production size basket with a capacity of 1,500 lbs. of product. Thus with 3-6 batches per hour, this small footprint Shaka® retort can process 4,500-9,000 lbs. of product per hour. Shaka® retorts can be designed to execute water spray, water immersion, steam, or steam-air-thermal processes. They accommodate such packaging types as cans, plastic cups, trays and bottles, pouches, cartons, glass jars and bottles, and smaller food service containers. Loading and unloading can be either manual or automatic.
Lower cook time – higher quality
This first chart shows the sterilization time differences among static, rotary, and Shaka® retorts in the preparation of pea and ham soup in a gusseted pouch. The Shaka® process represents an 84 percent reduction in retort time.

The photo shows the color differences of the finished product. The Shaka® processed soup has a much more natural and appealing color.
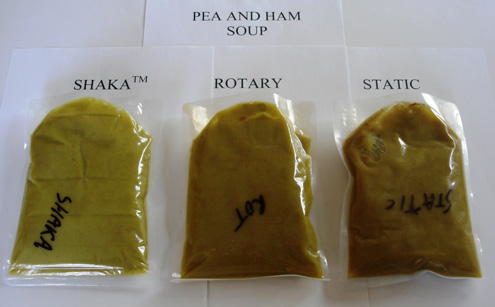
The following chart shows the processing time of a delicate food – white sauce in 300 X 406 cans.
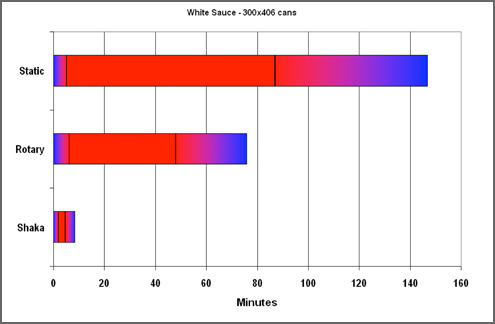
This image shows the more natural appearance of the Shaka® processed white sauce.
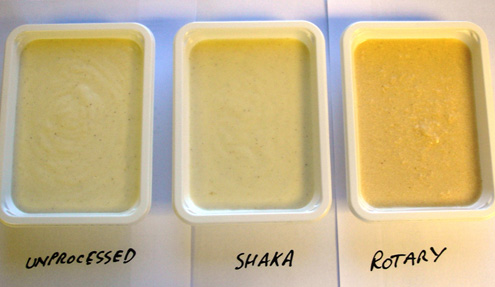
Shaka® process compared to UHT/aseptic packaging
Research carried out in recent years reveals that the quality of foods produced by the Shaka® process is equivalent to that produced by UHT processing/aseptic packaging. Taste, texture, color, nutrient retention, and cooking values over a range of products showed minimal differences between products aseptically processed and those Shaka® processed.
This may be somewhat surprising as UHT process sterilization times are usually measured in seconds whereas Shaka® process times are minutes. However, if the higher temperatures and the residence time for products passing through tubular or scraped surface heat exchangers in the aseptic process are taken into account, the overall heat exposures of foods in the two systems are similar.
The Shaka® process is inherently more flexible in terms of the range of food products it can handle. The Shaka® process, unlike UHT, can be used with foods containing particles, thus avoiding FDA and other regulatory limitations on particles. Anything thin enough to move within the container when agitated in a Shaka® retort will sterilize quickly and this includes soups, sauces, ready meals, dips, spreads, baby food, pet foods, etc.
Because Shaka® is a batch process, changing from one product or pack to another is simple. By comparison, UHT plants are generally very limited in the range of products effectively processed. For example, a UHT plant could be set up to process a range of flavored milks. To process milk based desserts would require radical and expensive changes. UHT processing requires product- and pack-specific aseptic packaging. This further limits the types of product that can be packed in a given plant.
UHT processing/aseptic packaging presents two further challenges: higher capital cost and complexity of operation. Capital costs are often confidential and difficult to determine with any accuracy. Research conducted for this report, however, suggests that UHT processing/aseptic packaging plants cost 50 to100 percent more than conventional packing lines utilizing retorts sterilization.
Both UHT processing plants and the aseptic fillers are much more complex systems than are generally present in most food packing plants. This can give rise to significant problems in recruiting and training existing or new staff. Commissioning periods of up to two years for UHT plants have been recorded as compared to 60 days for retorts.
This is not to say that UHT does not have its place. For high volume production of a limited range of similar products, in similar containers, for a large and established market, UHT can be an attractive option for a packer that masters the technology.
Changing the paradigm
While the quality of UHT shelf-stable food is unquestioned, the limited types of food that can be processed, high capital cost, and lack of flexibility severely restricts entry into this product category for many processors. Now with Shaka®, those constraints are gone. Food processors can enter aseptic food categories, bringing an array of new food products to market in eye catching and varied packaging. And they can do so in a fraction of the time and with less cost than the UHT lines.